Matchbox Studio
(03/05-10/16)
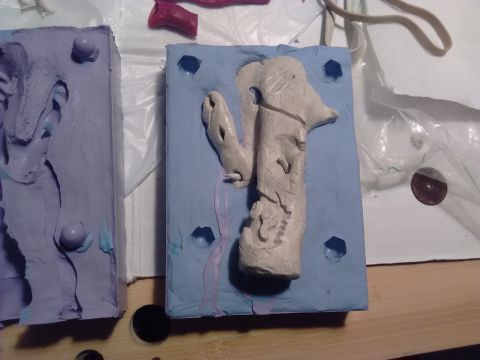
Over the weekend I set up to try out casting in resin, but first I wasted a few hours trying to recreate the plugs for the holes before moving on...
"Resin" is just an artsy way of saying "plastic" - a quart each of part A and part B...
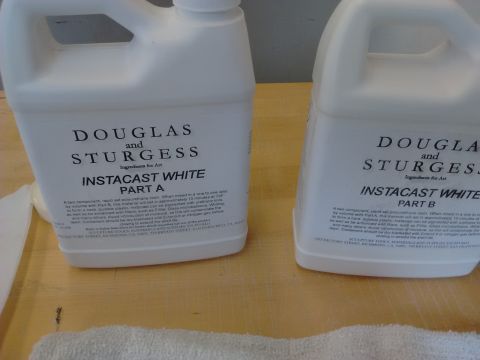
This product works really well with silicone molds and is moderately priced...
Anyway, I cast the first one on Sat., and because my studio was around seventy degrees, the thing solidified in ten minutes, looking great but screaming bright white...
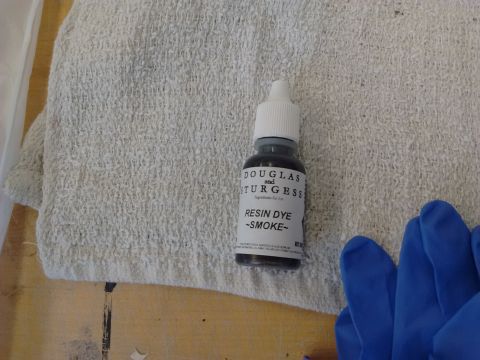
... so on Mon., I tried again with the smoke dye...
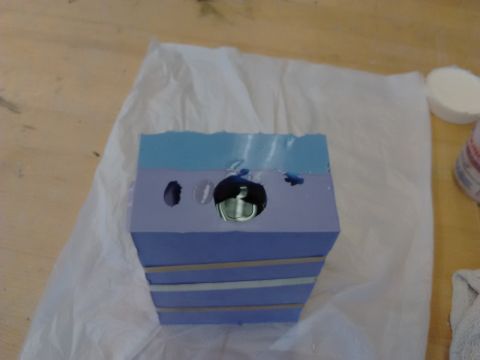
I did three pours and only on the last one did I get the timing right to demold the plastic when it's firm but still pliable enough to bore through those holes with a wax tool...
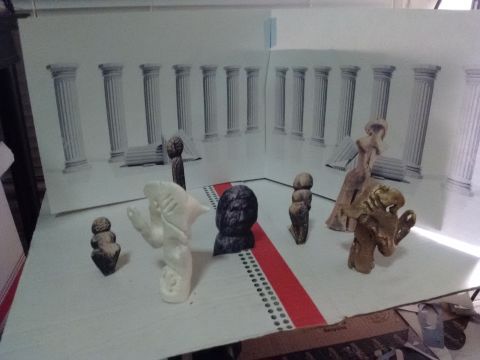
Tues. was a free 'flex' day, so I put the rest of the little diorama together for Wed. Sculpture class...
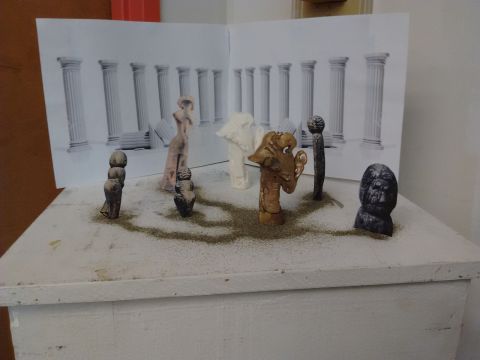
This is the setup in class for my critique. I got a few nice interpretations on the mythological subtexts behind these icons, but many students felt there was a story going on, strongly suggested by the sand. Cool. BTW, the piece is named "Avatar Trainee."
Definitely re-casting in bronze...
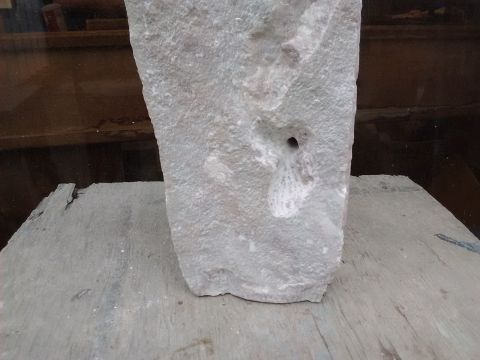
There was a pause in the spate of El Nino weather outside, so after my critique I hauled out the stone again. I wanted one more hole for the cave effect, and try to work out the interior angles...
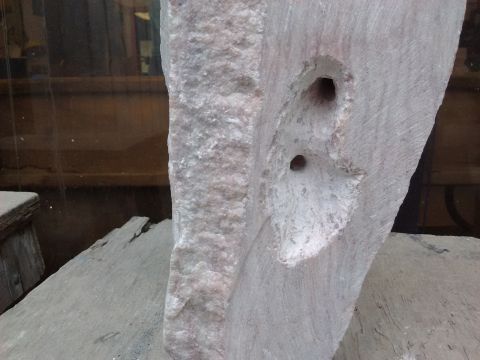
After the upper hole was drilled out I got a better idea of the negative space contours possible from this vantage...
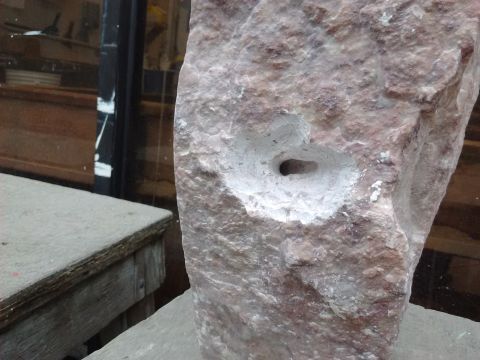
This angle doesn't really show it, but there's a kink in the opening I'm developing. The beginning and ending of the cave will extend elements to help shape the exterior and blend with the bottom-up method, based largely on what the stone says to me while I'm carving (no, I did not say 'stone whispering'...)
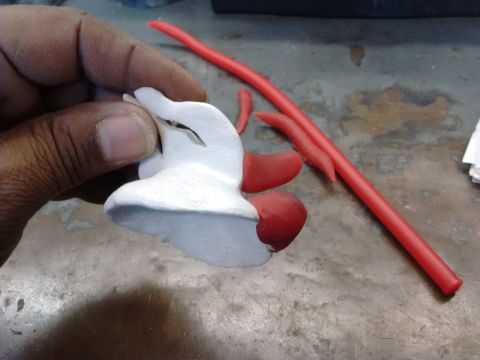
Today I slogged through the deluge to Casting class and setup to work on the last remaining parts of the first project - re-casting the bronze, and testing the ADC for direct casting. This 'hat' thing will go into a flask and we'll see...
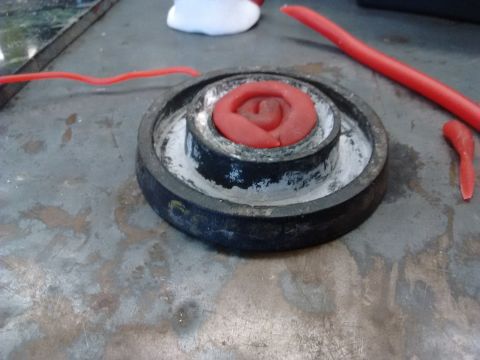
A broad base and thick sprues will help, but the concern is that the compact paper won't properly burn out, and the molten metal will pool and splash (the reason for gravity casting from now on)...
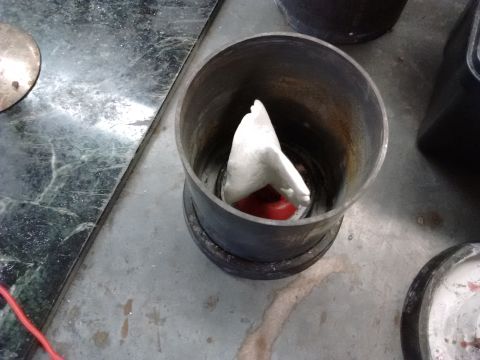
In the end I had to glue the thing to the wax before fitting the flask on.
While fiddling with the hat, I had the double-boiler going and hit the silicone mold with one one last red wax pour and gave it twenty minutes to cool...
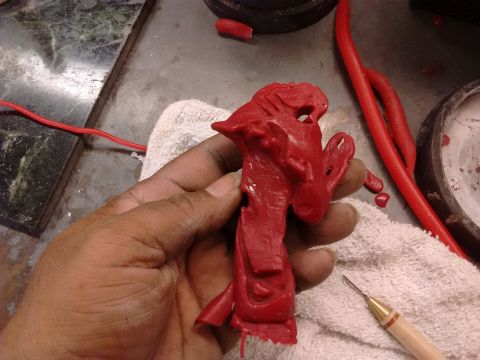
It came out looking good, but still only 90% on fine details. This casting wax is stretched with sprue wax, too...

It took too damn long to clean out the holes and trim the flashing...
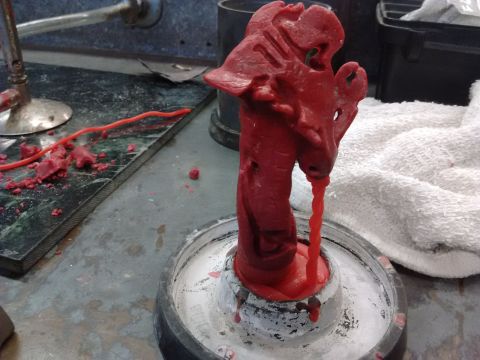
Ok, sprued, weighed and mounted, and we had fifteen minutes of class left. Into the shop locker it went, and I'll deal with it on Tues...