(12/10/15)
The pile is what was left after the bed was swapped for the camp cot. I thought I could work around the inconvenience but it was a real headache. With the holidays now upon us, a sale provided the resin storage shelves seen below, and the pile is now organized with room to spare, and my studio is running much smoother.
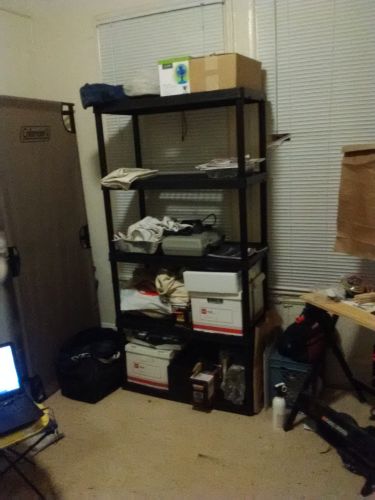
That's great, 'cause I got two big projects to do this weekend - Bi-Metal and a re-do of the Large Casting project...

The Bi-Metal Project is basically casting one metal (in my case, Sterling Silver) onto another (Stainless Steel) with the option of also casting a stone 'in place.' I attempted this with a Cubic Zirconium...
First I came up with an abstract design...
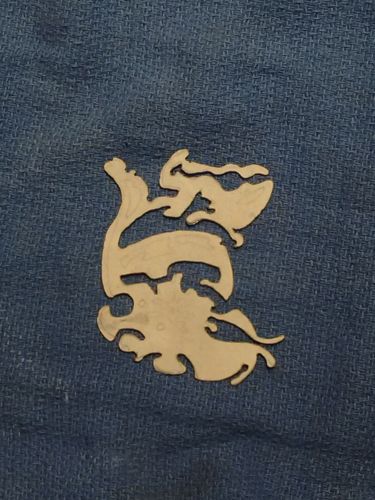
Then I used a jewelry saw to cut out the steel pattern...
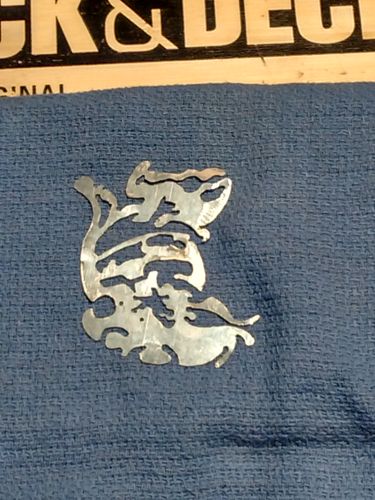
Because I didn't have any self-stick blank labels to use, I improvised with spray adhesive which I had to slowly peel off to prevent bending the delicate steel...

Here semi-firm brown casting wax is added to the steel...

The wax is tightened up a bit, but left largely unfinished, Usually you'd do the opposite, but the steel is so thin it wouldn't bear handling, which manifested during the spruing part...
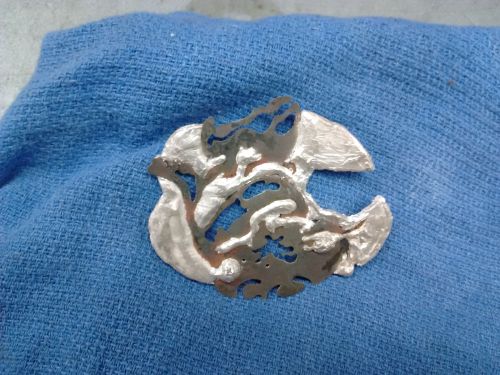
This is the result from casting day, which was our last day to cast. The steel ain't shiny, and in fact it warped a bit somewhere in the process, but the silver's holding it just fine. It's easier to see the stone-like quality of the silver, and what has to be transformed...
(12/18/15)
Yesterday I picked up my Metal Arts projects and formally closed out the Fall term. For our final critique we also present a display element, which explains the swatch of leather used to make the Bi-Metal piece stand out. The paper there is my grade with comments...
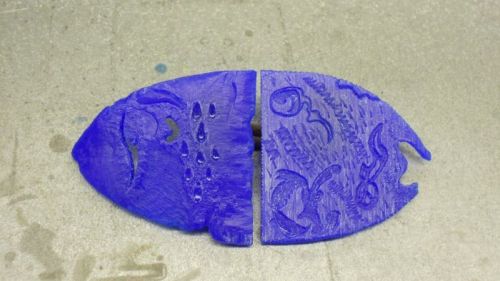
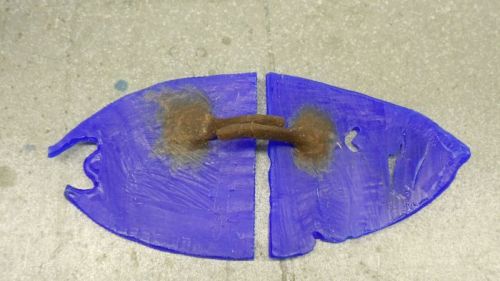
The second project was a 'Large Casting' that required the use of a vacuum casting machine. It actually came before the Bi-Metal, so, long story short, I carved these two abstract forms from hard blue wax, came up with back pieces to aid in the display, lovingly put wax sprues to the thing and invested it, and when I got to the actual casting the molten bronze backed up and cooled before the pour finished. One piece was half cast; the other was a big brass hockey puck. with 10 days left (3 class days, actually) I had to pull a re-do...
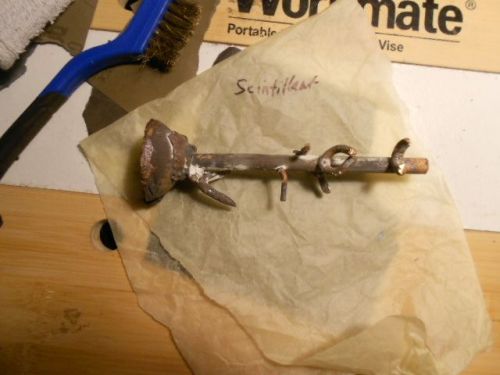
I grabbed more of the semi-firm brown wax and fashioned two new forms, carved more designs and got them prepared on the last investing day. The casting flask I used for this attempt was much larger, so I had to sit out the next to last casting session so the beginners could have their freakout day...
Anyway, on the last casting day I did both projects, but this one had me sweating. the pour went smooth ("Adamantium reservoirs drained"), no hockey puck on top, just the proper sprue button. After quenching the hot flask in hot water (don't do this in the sink unless you want to fund your plumber's next vacation), it came out beautifully, 95%. That's the sprue 'tree' I spent that weekend cutting off...
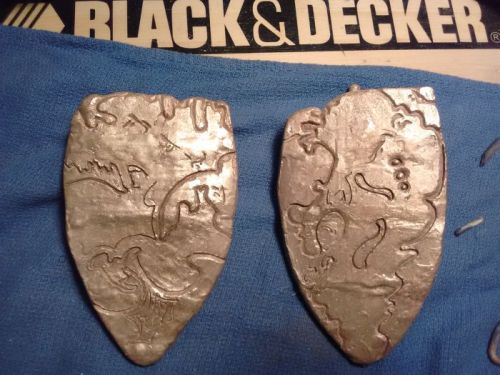
The cast pieces came out funky and rough. The back pieces are where that 5% failed, but a trip to the hardware store for a little hose clamp did the trick...
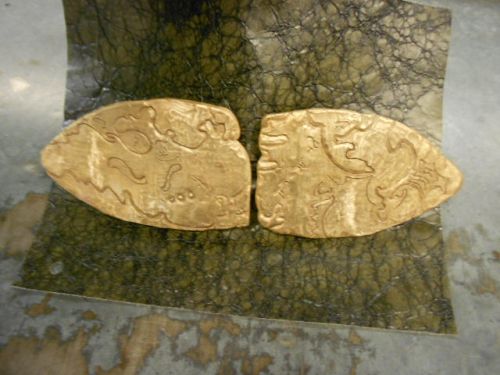
For presentation I plan to mount the piece in a frame (the craft store didn't have) with that larger swatch of leather. The class dug the piece, some insisted that 'it could be a necklace.' Yeah, at Burning Man...
At the end of the day, I have one piece as inspiration for further bi-metal work, and one piece that will go into the portfolio when it's finished. Cool...