Matchbox Studio
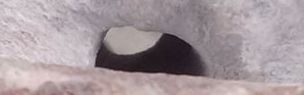
(05/04/16)
Yeah, the Symposium was great and a unique opportunity as a young sculptor, but I return with three weeks of class and studio time left and too much to do, but that's what May always is - crunch time!
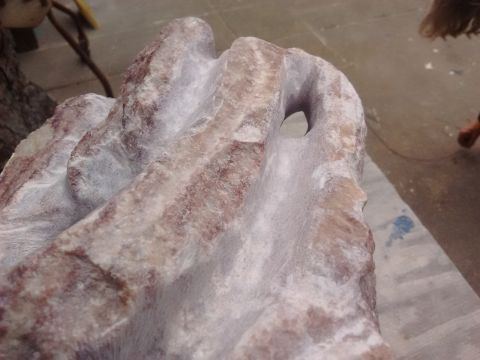
Though it's Wed. class, Mon.'s pics came late due to the long day of travel - I was still walking a step slower to class, and Stephanie and Alex looked like they hadn't slept. I decided to just concentrate on getting rid of those perfect circle drill holes...
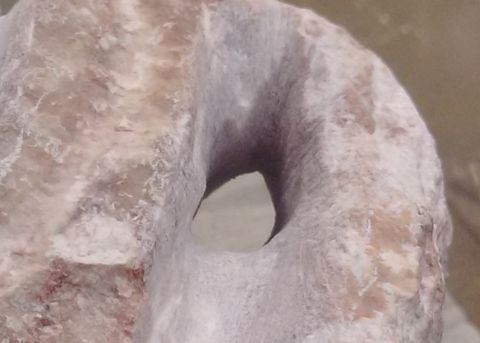
Using a small carbide bit with a power drill and the new riffler, the contours open up...
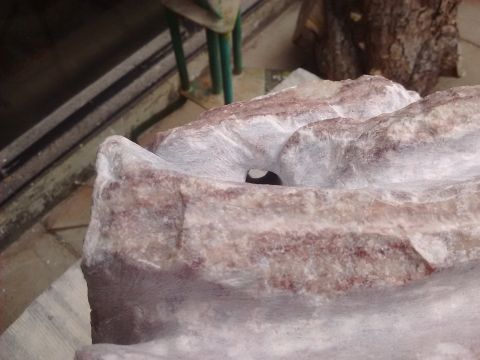
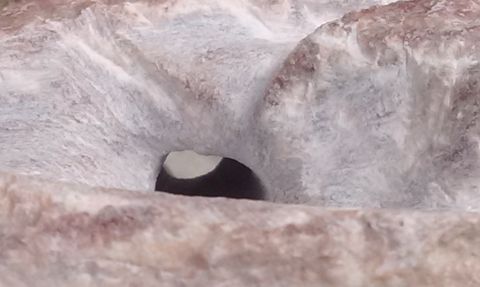
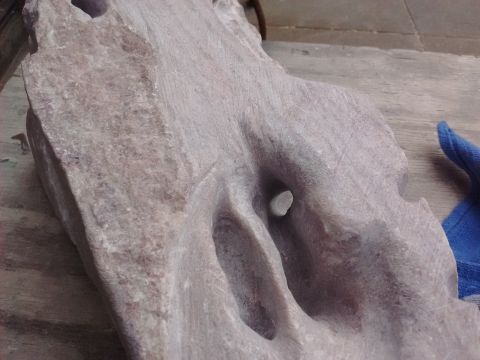
The new riffler really helps here...
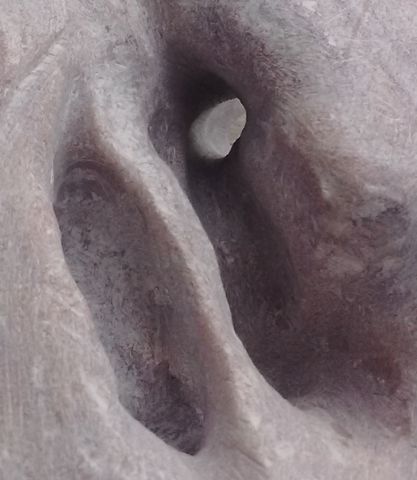
This interior is the last place I'll do any carving, and not until I'm at 600 - 800 grit sanding on the exterior. I've already broken through the center element in back, but I'm not freeing that floating column until time to sand it, gently...
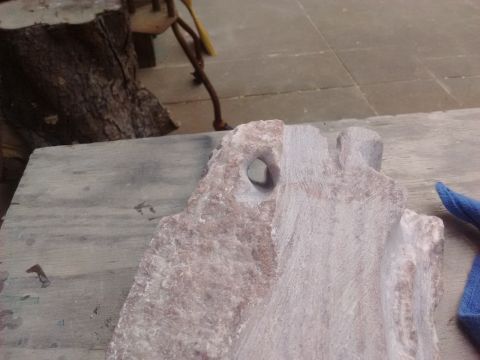
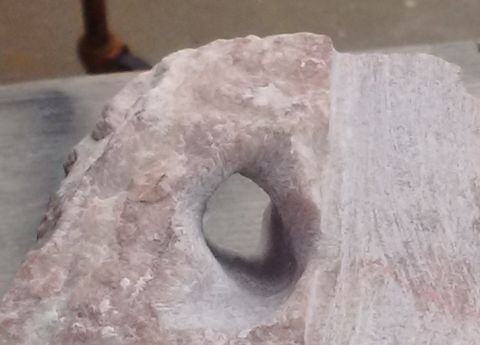
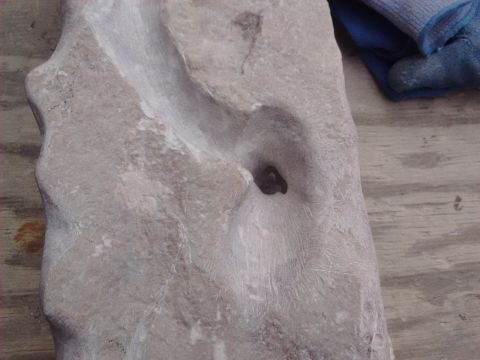
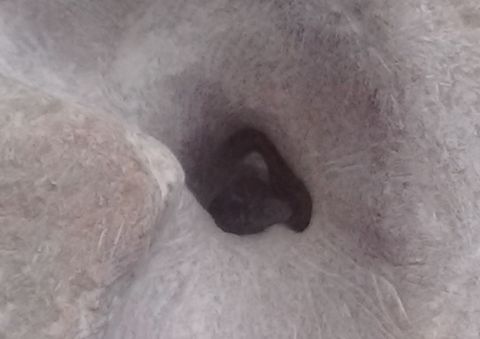
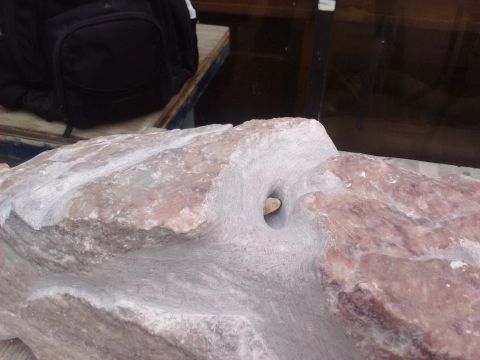
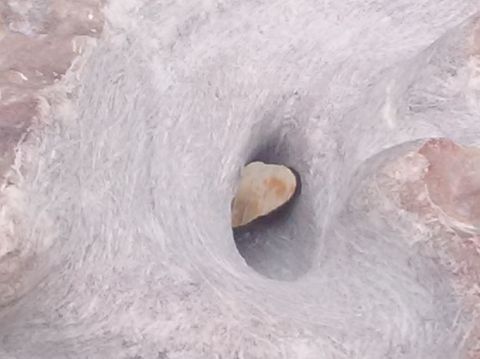
Today it's back in the sculpture studio for a last bit of outside contouring, then I'm swapping it out with the clorite. This raspberry stone is going home to start sanding, and the other piece will need power tools to get all those blanks cut out and defined in time; too noisy for the home studio...
Oh, Casting class? Yesterday I took the funky bracelet in and refined it for a couple hours, then invested it. Pictures, if any, after casting....
(05/06/16)
Well, Friday is still crunch time, but with progress to note...
The big stone's exterior contouring with the power drill went well before lugging it home in the cloth Goodwill bag. A little more work with the flex shaft, then the sanding begins...
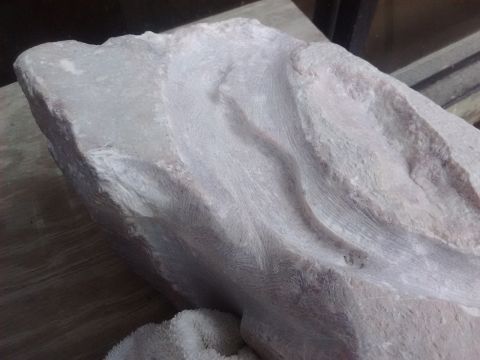
The swapped in chlorite looks awfully raw in the light; the power drill will have to chisel out all the elements inside and out next week...
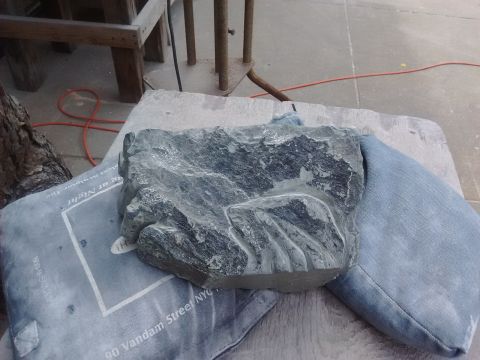
In Casting, I checked the flask and fired up the electromelt kiln, then worked on the delicate waxes for the 'jewelry set' project...
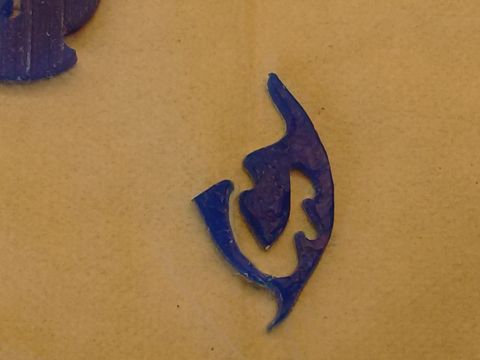
The upper piece is the ear ring; the lower a pendant. Both pieces are in two pieces that'll be addressed in the spruing, and maybe I'll have enough silver left to cast them...
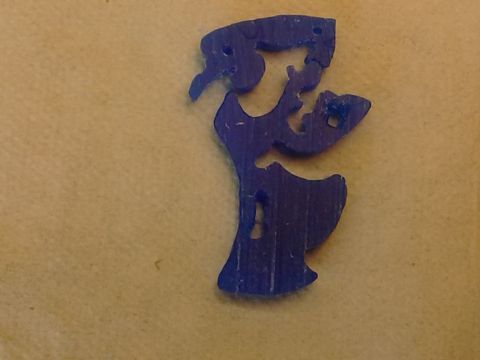
The bracelet was gravity cast in bronze. I was concerned about possible metal gaps because I deliberately left air vent sprues off the outside of the bracelet, but the gamble paid off...
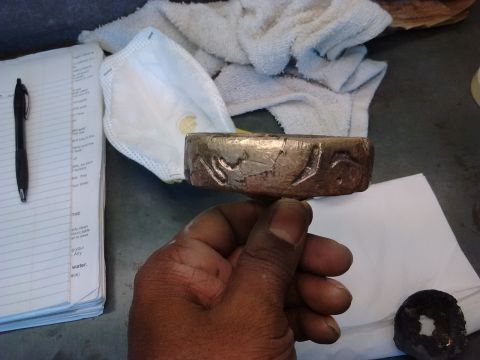
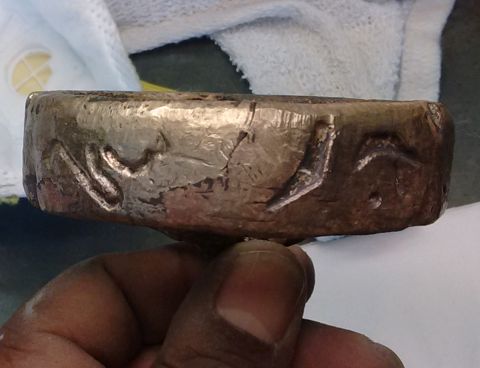
This is fresh from the flask and washed off; the pickle and refining comes next...
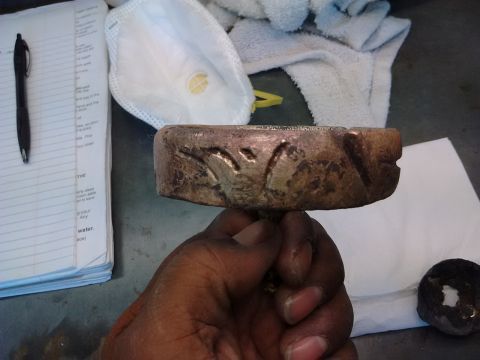
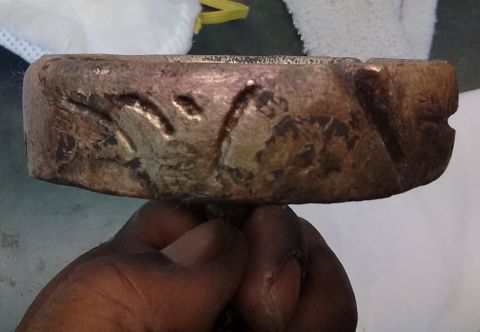
So, with my work cut out, I won't be bike riding this weekend, and Screenwriting class has its own drama because our teacher had to go to the hospital, and we have a replacement coming on Monday. Again, typical for crunch time...
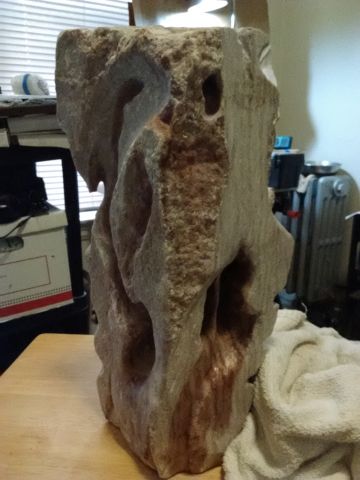
(05/08/16)
Friday was a day to rest and plan the sanding for the big stone to get a good blend of polished and natural textures. I washed the dust off the stone and brought out the colors...
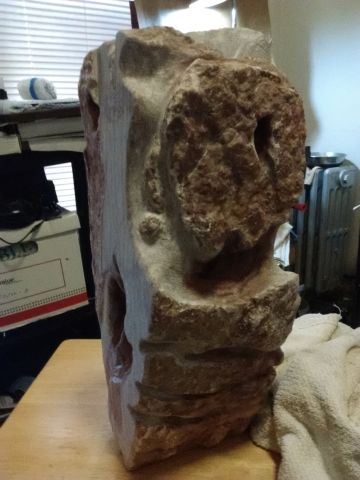
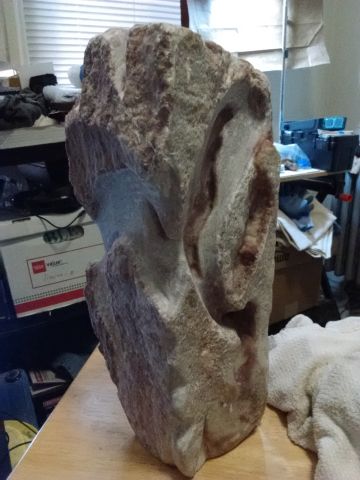
The natural textures have to be broken through with sanding, otherwise that boring solid rock side throws the piece off balance more than I want...
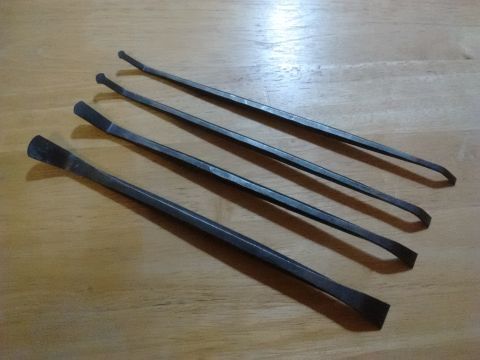
So, Fri. and Sat. I broke out the set of 'Raschietti Scrapers,' specialized chisels based on Old School Italian artisan designs, to skip past those early grits and jump right to 220. So far they really come in handy on riffler marks and adding contours to the flat planes on the stone...
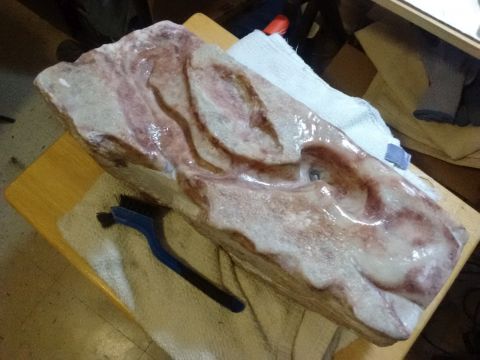
This is a Sun. pic of the results so far after another washing...
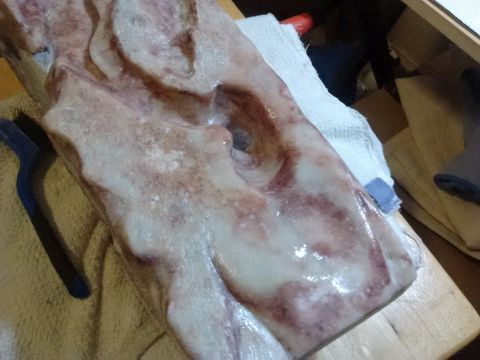
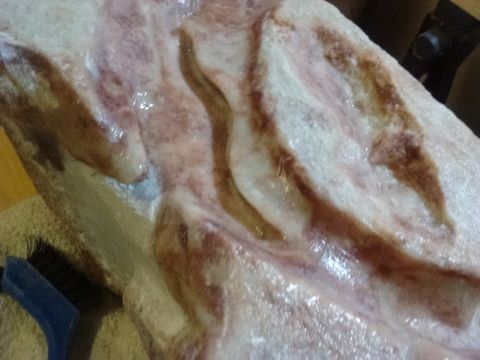
The contrast will be stronger on the opposite face...
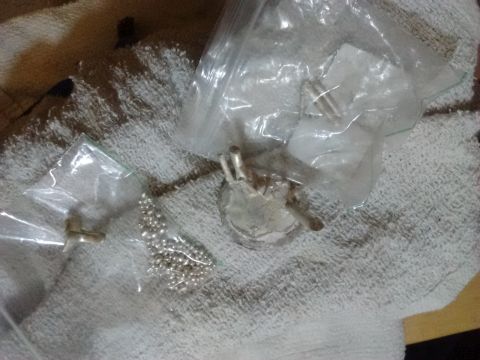
Meanwhile I dug through my stuff for silver scrap and got 150 grams - enough for the pendant and earring in the jewelry set...
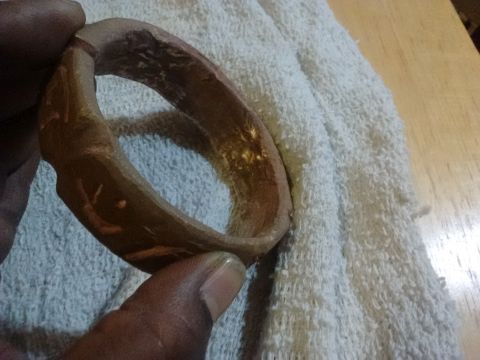
The bronze bracelet was worked on Sat. - the sprues were cut off and ground down then the big piece went into the pickle pot for almost an hour to cook off the oxidation.
The piece will get another scrubbing with dish liquid, then I can start with the 220 grit, probably two or three sessions before moving on....
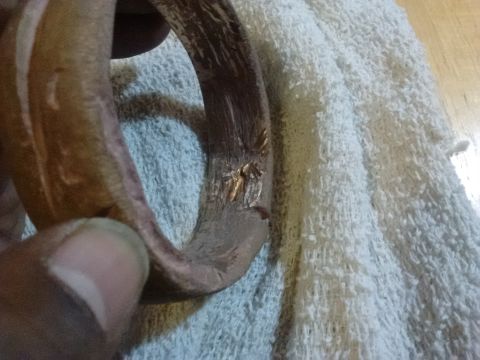
Today I have the jewelry waxes and the screenplay to work on, then I'll think about the chlorite stone work tomorrow
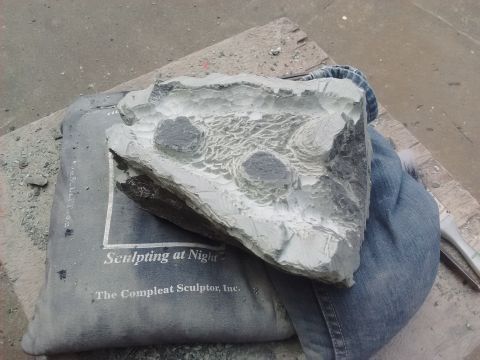
(05/13/16)
Ok, this triskadeksfragalistic Friday is where crunch turns to crisis as I speed toward the climax of finals week on the 23rd. Screenwriting class needs another five pages of script to complete Act I, which should be a piece of cake (yeah right); Sculpture Studio has the two stones; Casting has the two remaining projects. And no bike riding this weekend...
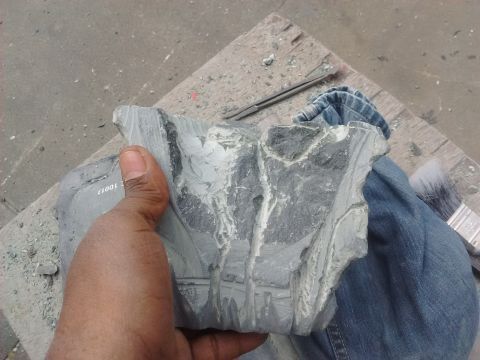
Teacher Stephanie was out sick on Monday, so instead of waiting an hour to get into the tool room for the power drill, I attacked the chlorite with chisels to carve out the design elements. Each side was pared down gingerly...
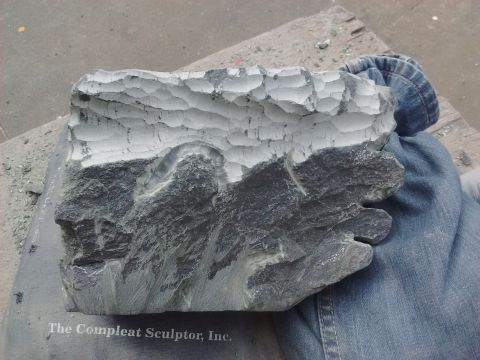
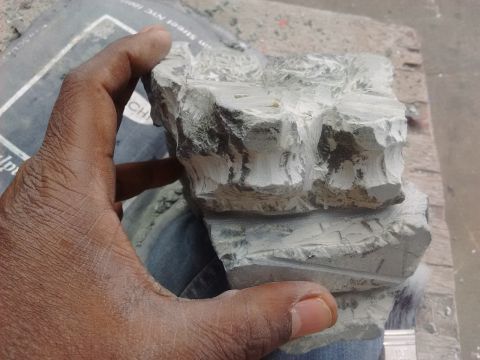

Tuesday in Casting began with final prep on the jewelry set...
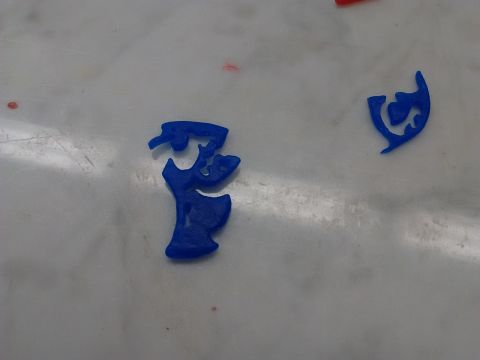
The earring and pendant, still in pieces, were smoothed out a bit, then set in place using wax sprues..
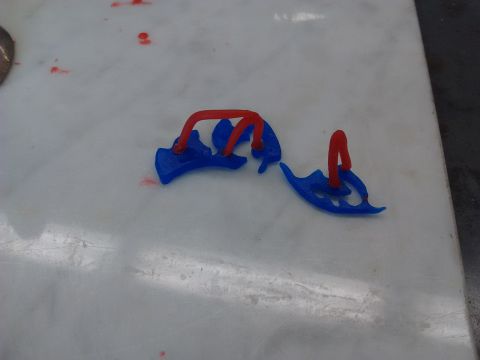
The pieces were reattached and added to the sprue tree and in the flask...
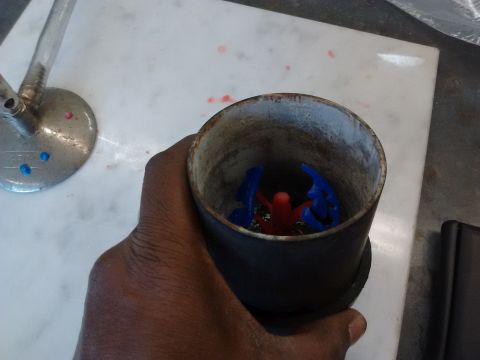
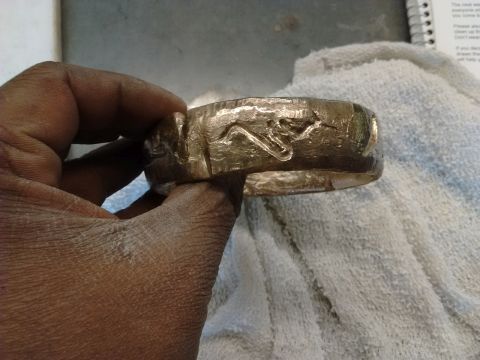
While waiting my turn at the investment station, I scrubbed the remaining pickle dust off the bronze bracelet with a metal brush on the flex shaft...
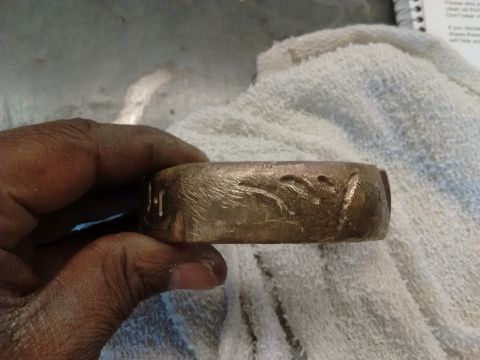
I'm considering melting a bit of silver into some of the 'letters' with solder...
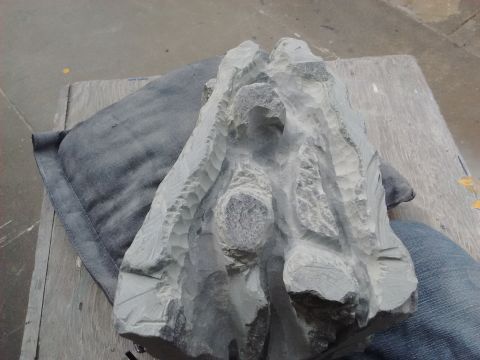
On Wednesday I got the corded power drill and managed to get some serious gouging in with an assortment of carbide and masonry bits...
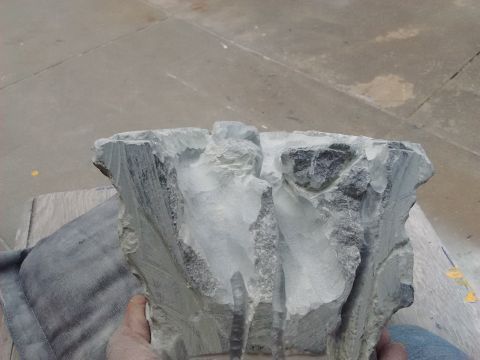
This much removal of material from the top and front with the chisels would almost certainly have splintered the stone into two or three chunks...
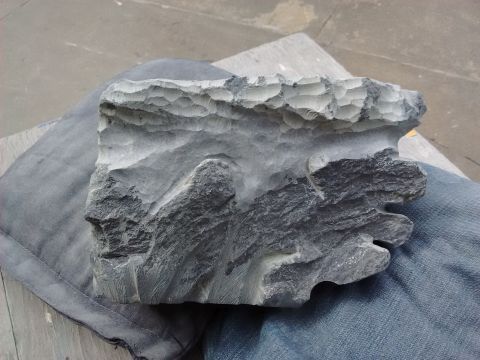
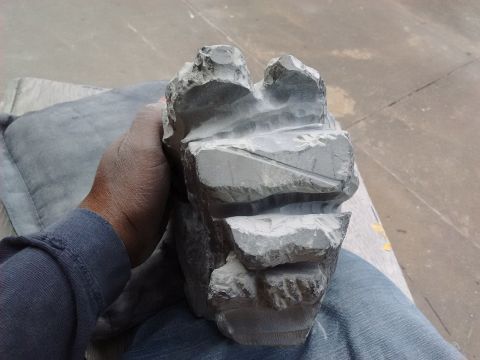
The stone at this point is finally getting past 1st base. After three hours and a cloud of swirling chlorite dust, most of the design elements are established, but I decided to bring the stone home, so into my art dept. locker it went for pickup the next day...
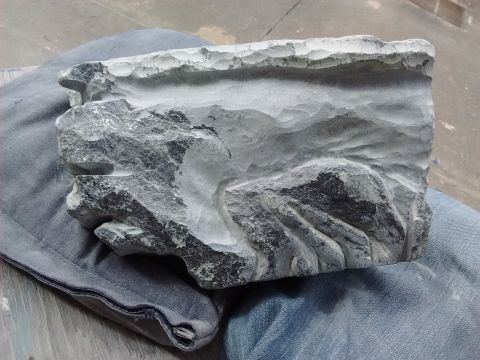
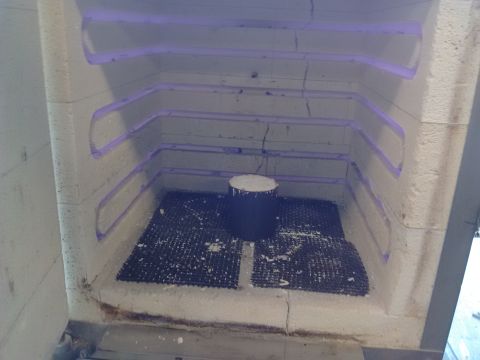
Thursday I was casting my lone flask with the scavenged silver - turn on the electromelt, heat to 1900 degrees, toss in the silver and check it in 15 minutes...
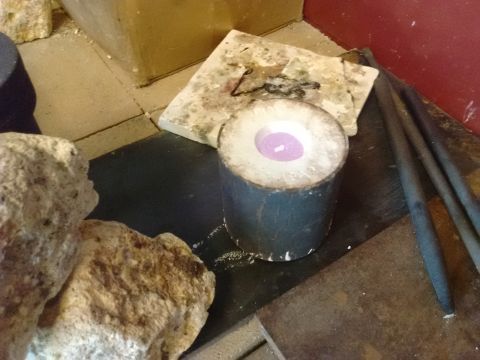
The metal was liquid at first check, so with a little help the flask was placed beside the melter and I got a clean smooth pour. Shutting off the kiln and melter marked the end of heavy lifting...
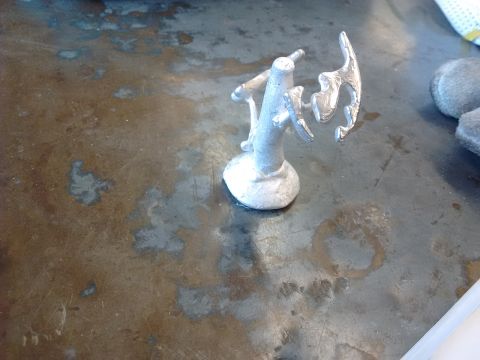
Sonofa... After washing the investment and casting out of the flask, the damage was plain to see - 70% success Two sprues detatched from the pendant and the earring remained in two pieces. This has happened to everybody in class behind these friggin' sprues. I put it in the pickle while going over salvage options...
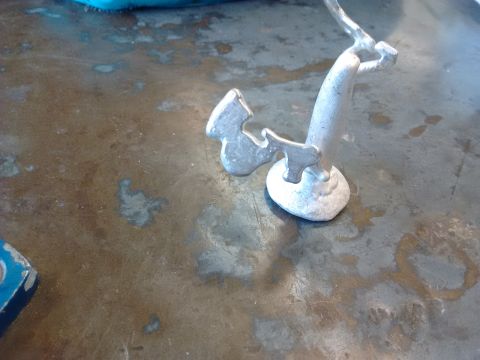
I have enough silver in that sprue tree to attempt a redo, with the suggestion to bolster the flimsy sprues with some casting wax. Anyway, I brought it home to see whether or not to save these bits or completely redo. 10 days and counting...
(05/15/16)
The rest of Friday and Saturday morning was spent on the big stone, finishing up with the scrapers and deciding how to sand it to bring out the contrast in textures...
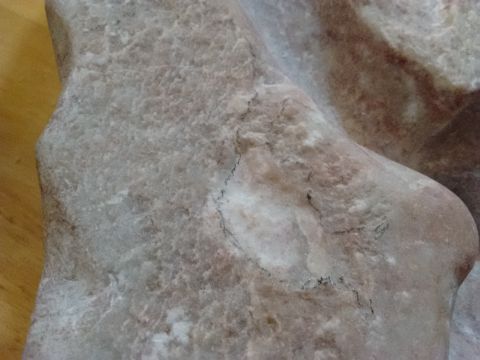
The stone will end up 50/50 polished and raw, with solid pencil lines marking a hard design border...
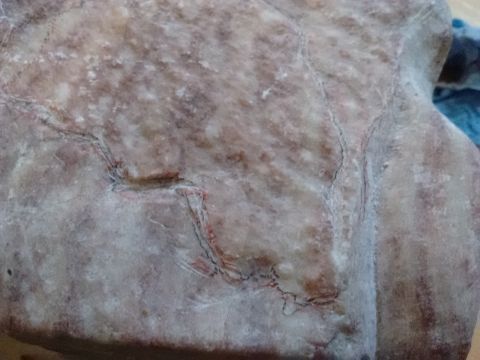
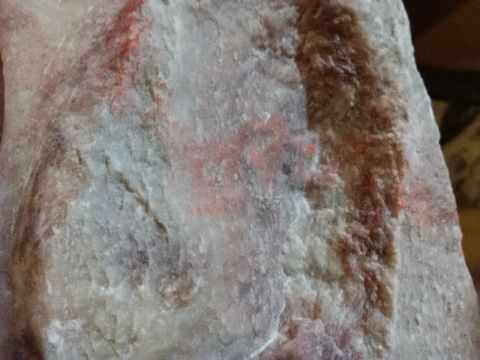
The area here has a broad red crayon border where the aim is to taper the sanding from smooth to natural...
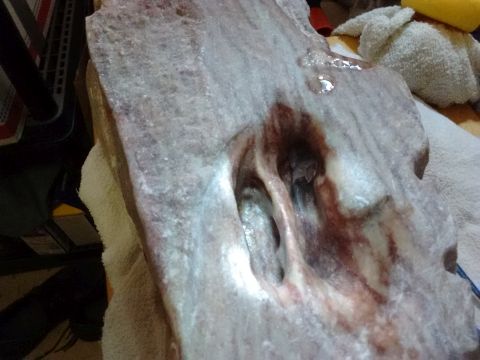
The final piece of carving was opening up the 'cave' and freeing the column...
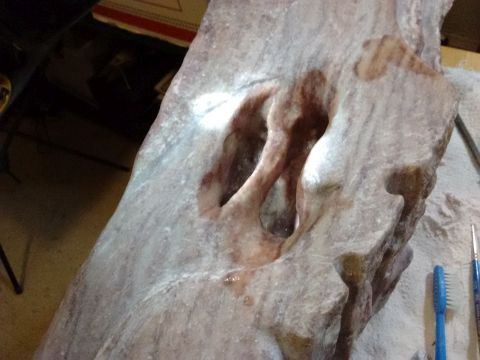
I might taper the sanding of the column, but the interior will get the full treatment to help it stand out...
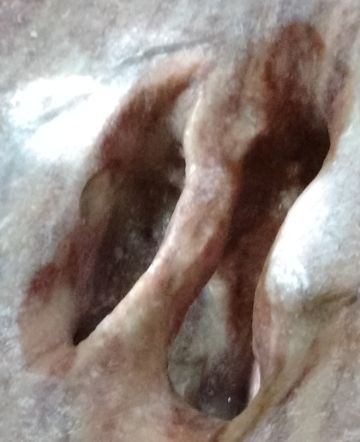
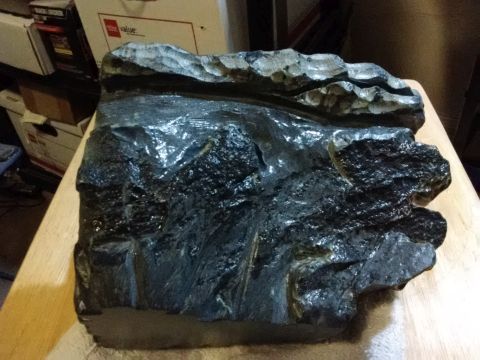
Just finished for the day. The chlorite got the dremel treatment to free more of the elements. I can't use the power drill like I'd prefer, but this goes a long way to make tomorrow's session go faster. After carving and gouging for a couple hours, washing the stone brings out the deep ebony...
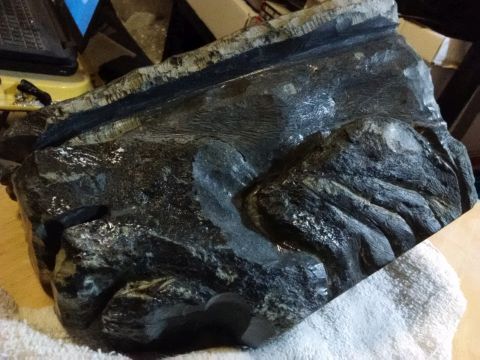
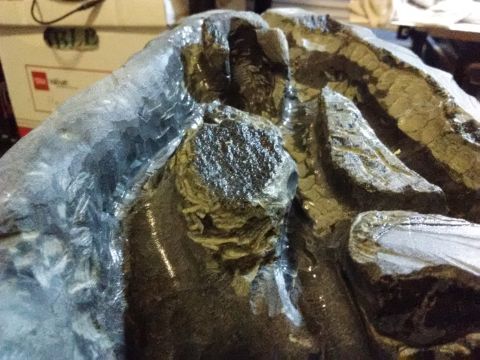
The elements on top are almost there, even with running the dremel on low speed...
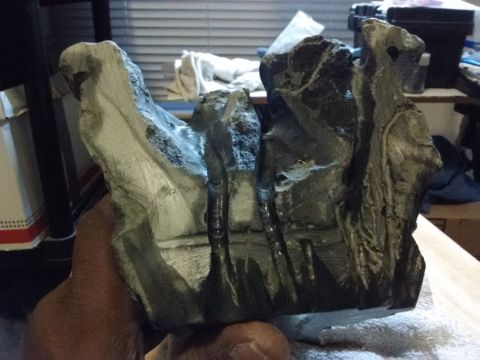
The double studio schedule suggested by a few carvers at CSS - to work on two stones at once - seemed to work well. Three hours in both the morning and afternoon, separated by a 3-4 hour break, isn't a strain. I'll need to work this kind of pace to build up that starter set of show pieces, along with looking for 'shelf space' for the few works I'll have when I finish art school. So yeah, I'm hunting down shows with small entrance fees for this summer and fall...
(05/17/16)
The chlorite went back to school where I used the dremel on high speed to finish cutting out the elements started at home on low speed...

After another session of swirling clouds of green dust in the light breeze, I switched to a couple masonry bits and smoothed out the remaining rough bark of stone on the sides...
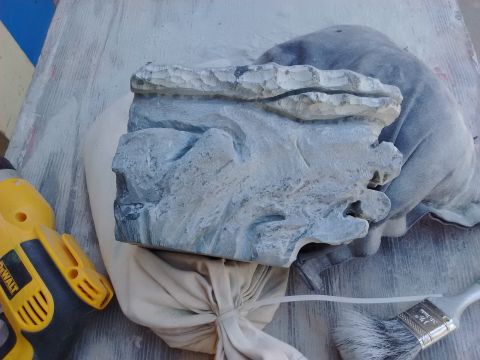
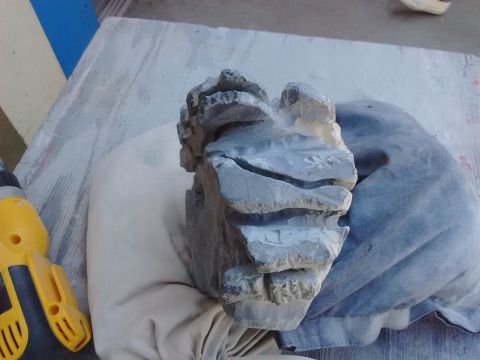
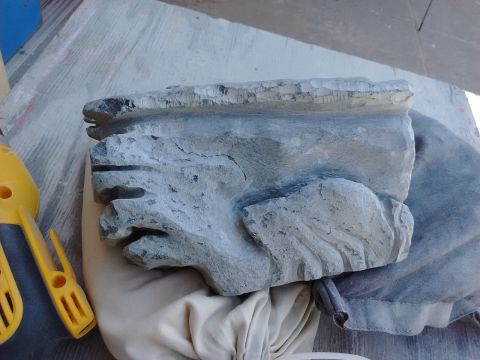
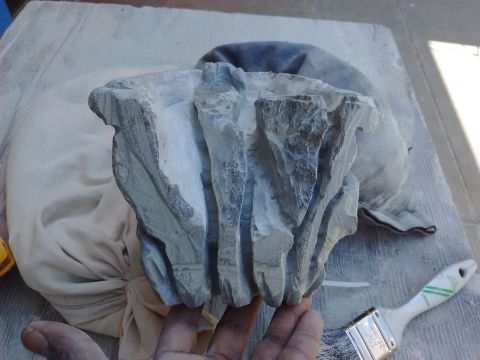
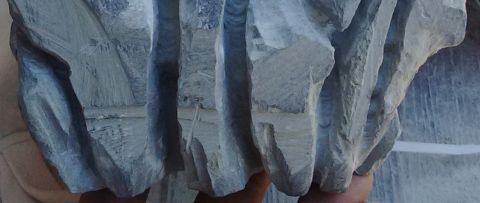
(05/20/16)
Today marks the final weekend crunch of working all the projects to completion, so no more pics on these pieces after this posting...
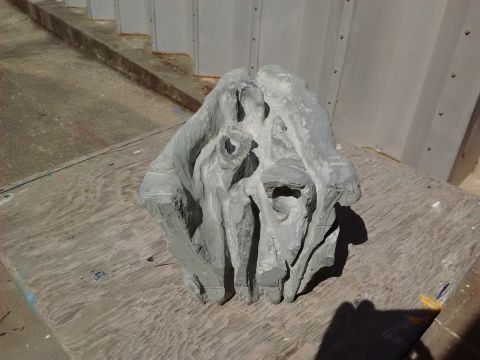
The chlorite has the major elements carved out now, ready for refining...
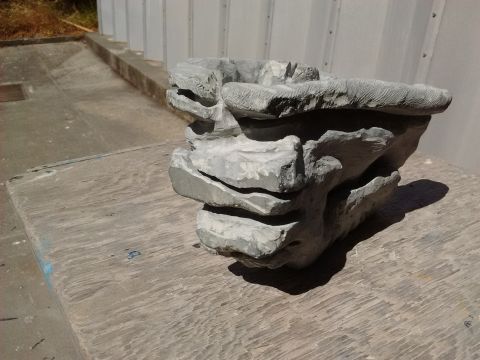
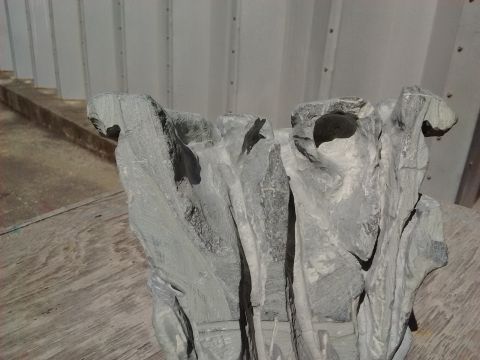
The rifflers have already knocked some of these hard edges smooth and contoured...
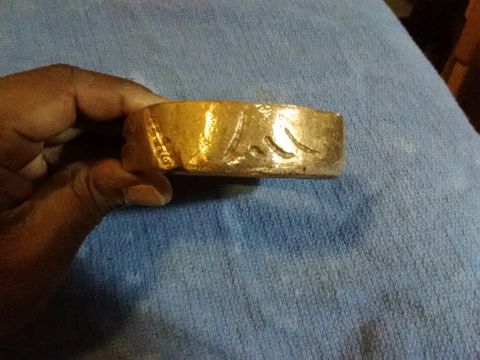
The big metals push is the jewelry set - grinding and sanding the bronze bracelet and finishing the 11th-hour replacement pendant and earrings...
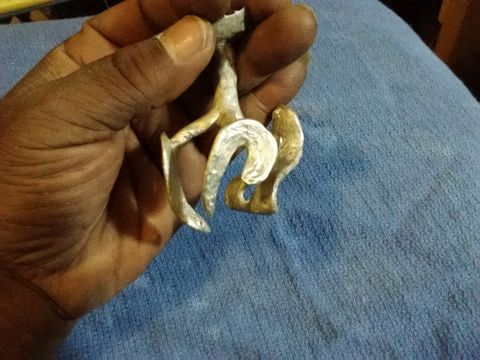
With one day to create wax pieces to invest, I decided to try an ancient design look with a textured surface...
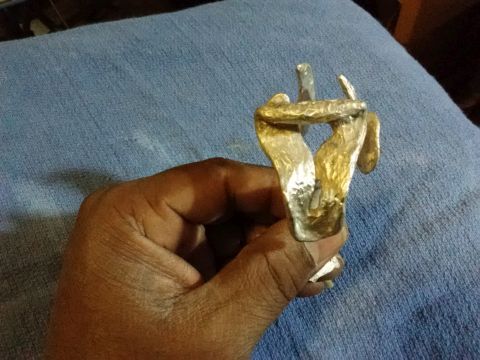
The pieces will have a few abstract 'letters' from the ring and bracelet carved into them to tie the pieces together...
While working the metal and two stones, I also have the last five or six pages of screenplay to write for the remaining final, so my work is cut out. Cool...